Solar energy is an option among renewable energy sources that has rapidly increased in popularity in recent years. Turkey's sunshine duration and geographical advantages make this resource even more attractive.
In order to maximize the benefits of solar energy, a plant design and installation process that prioritizes safety is of utmost importance. Occupational safety measures must be carefully planned and implemented to protect the health of employees and to ensure a safe and sustainable energy source.
In this article, we will discuss the basic stages of rooftop solar power plant installation, the main hazards foreseen in the processes and their occupational safety measures.

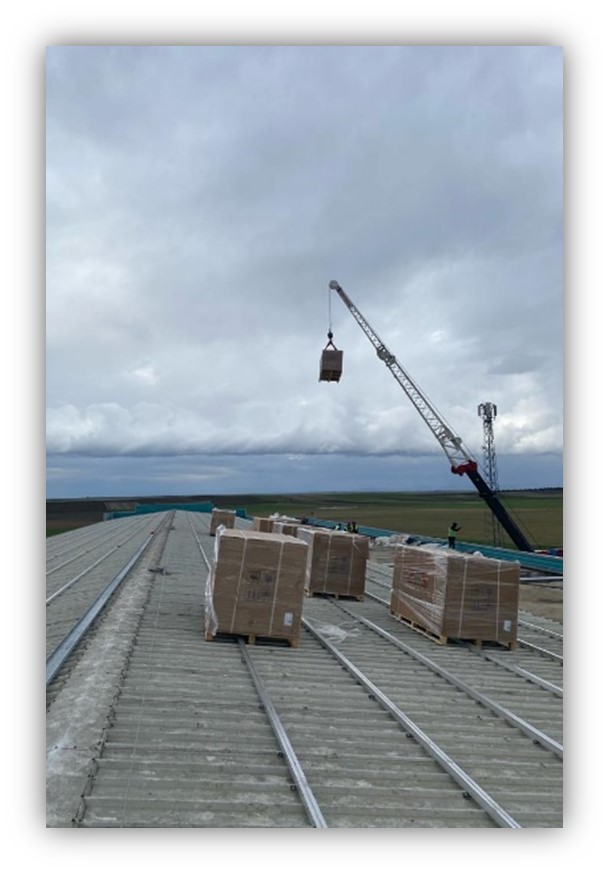
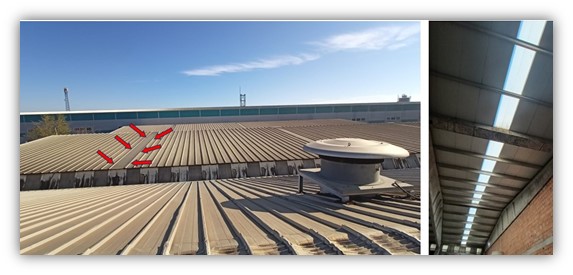
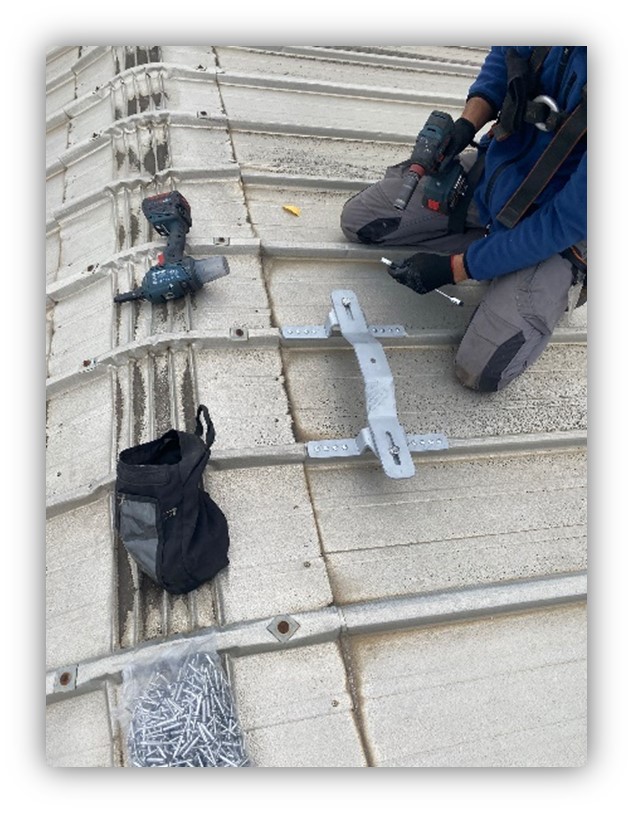
Stages of Solar Power Plant Installation
- Planning (Project Design and Layout Design)
- Assembly Phase (Field Activities)
- Tests and Commissioning
- Plant Operation and Maintenance
A. PLANNING PHASE
A.1. Panel and inverter calculations
When there is a mismatch between solar panels and inverters, high voltage and current can be generated when the power plant is operating due to high voltage, but the values may still be outside the legal limits. Or, when sufficient voltage and current are not generated, the power plant may not operate properly and cannot provide enough electricity. Since the weather conditions of the region where the project is built can affect the solar panel and inverter calculations, the planning of the power plant should be done taking into account the terrain and climatic conditions. The use of DC and AC fuses for the protection of panels and inverters, the calculation of grounding and lightning protection systems should be checked. As İLTEKNO, we use simulation programs such as PVSol and PVSYST in project designs.
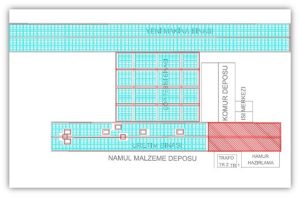
A.2. Weather Conditions - Environmental Factors
Incorrect evaluation of environmental factors during project design or neglecting them in favor of a more economical design can lead to faulty installations. During the project design and planning phases, feasibility analysis must first be carried out and necessary permits must be obtained. The feasibility analysis is a preliminary preparation for the installation of the power plant by examining factors such as annual sunshine duration, temperature, rainfall, snow load and seismic conditions in the location where the power plant will be installed. Among the issues to be considered during the design phase are the solar panel and inverter model to be selected and the processes to be followed during installation. In our country, snow load calculations of structures are generally made according to TS-498 standard. Another point to be considered for solar power plants is the construction design and the tilt angle of the panels. If a roof-type solar power plant is placed in line with the roof slope, the application of TS-498 is sufficient. However, if the panel slope and roof slope differ, relying only on TS-498 may be insufficient in terms of snow and wind load. The use of Euro Code - 1 standard for solar power plants with different slopes and classified as special structures can prevent possible risks. The structural design of solar power plants is based on operational requirements and Turkish Standards (TS). The regulations and standards used are as follows:- DBYYHY 2007, Regulation on Structures to be Built in Earthquake Zones,
- TS 648 Standard on Steel Structures
- TS 498 Standard on Building Loads
- ASD 96 Cold Formed Steel Design
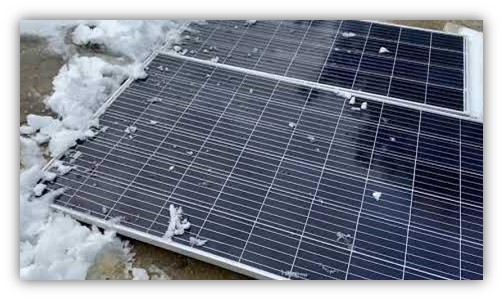
A.3. Power Plant Design and Technical Calculations
If the existing energy infrastructure of the facility is inadequate or in disrepair, it will create problems in terms of additional loads that will arise after the installation of the power plant. Electrical and data cables for lighting and air conditioning systems, especially in roof sections, should be distributed over a single line as much as possible and placed in cable ducts. In this context, it is of great importance to lay photovoltaic panel cables at the furthest point from the existing lines. In addition, a single line diagram of the facility must be obtained and analyzed. In addition, since the weight of the panels, constructions, panels and transformer cells and other equipment will put a very serious load on the roof, the structural analysis of the roof must be taken into consideration during the project design phase. It should be thoroughly checked whether there is any update in the project of the building where the project will be implemented and whether there is a need for reinforcement. In rooftop power plants, inverters are usually installed at ground level and connected via cable trays coming from the roof. In this context, in buildings they are usually placed in enclosed areas on the ground floor, and in factories they are placed on the wall adjacent to the structure. There should be absolutely no connection between the power plant electrical systems and the electrical installations of the existing structure; otherwise, there may be a risk of electrical fire.A.4. Procurement of Project Elements / Purchases
When uncertified materials are used in product testing and certification, the possibility of damage to employees and equipment increases during installation and commissioning of the power plant. When selecting products, it is important to pay attention to market conditions and customer criteria, and to clearly inform the stakeholders who will undertake the project about these criteria. In the selection of equipment such as photovoltaic panels / inverters / transformers / medium voltage cells etc. to be used in solar power plants; it should be taken into consideration that the manufacturer or distributor companies to be supplied have product liability policies. Similarly, the companies that will carry out the manufacturing should have professional liability policies. Therefore, liability policies should be sought in all companies involved in the process, including project design / product supply / manufacturing / operation. Some relevant standards required for the products to be supplied;- For PV; IEC 61215, IEC 61730, IEC 61701, IEC 62804
- For inverters; IEC 62548, IEC 62109, IEC 61727
A.5. Permit Processes
Design and site assembly should not start without an EIA report (or a letter of exemption) and a call letter.B. ASSEMBLY PHASE
B1. Logistics / Transportation (Bringing Equipment to Site)
Many risk factors should be taken into consideration during the transportation of project elements to the site. During the transportation of the panels to the site, occupational safety risks may occur due to damage due to lifting operations or bad road conditions, theft, bringing inappropriate equipment to the site, causing delays in the project deadline and additional costs.B1.1. Lifting Operations
Especially in roof projects, the transportation of panels to the roof requires serious planning. Scattered loading of panels on the roof will create an unsafe working environment and pose a danger to employee health. The physical condition, capacities, periodic controls and maintenance reports of the lifting apparatus used during loading should be checked. All areas that may cause danger during lifting operations must be restricted and unauthorized access must be prevented. Communication with the operator must be fully ensured.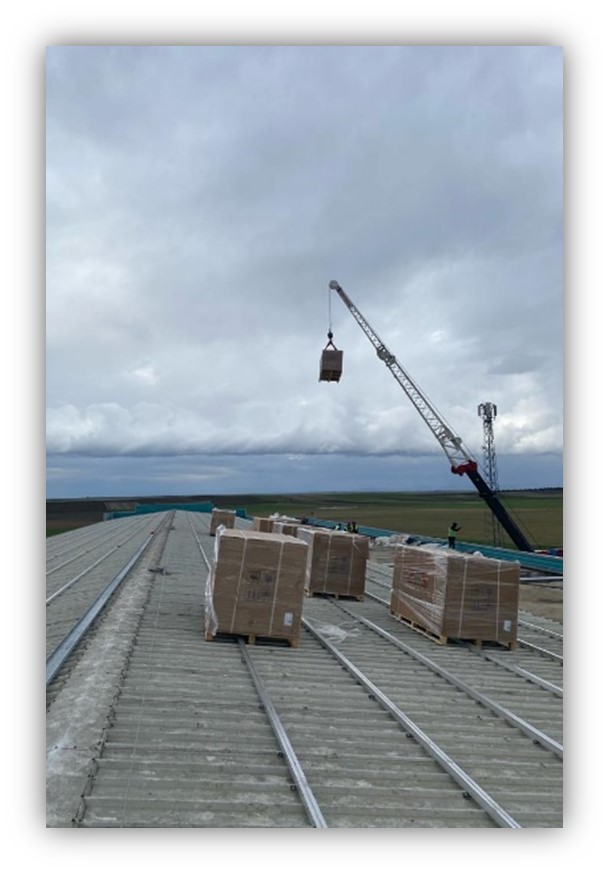
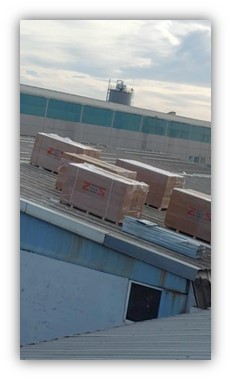
B.1.2. Theft
Cables should be brought to the construction site at the closest time interval to the installation, cable installation should be done immediately, cable ducts should be covered after installation. Reels should be stored in a locked warehouse to be created within the construction site.B.1.3. Road Condition
Tonnage vehicles bringing materials to the site, unsafe or delayed deliveries due to poor road conditions, overturning of heavy tonnage construction machinery and/or materials, etc. Before signing the contract with the customer, the project site should be checked and it should be examined whether the entrance and exit of heavy tonnage vehicles to the site is appropriate in terms of logistics. In projects located in the city, the traffic situation should also be taken into consideration during the loading of materials on the roof. If necessary, obtaining the necessary permits to close the traffic for a certain period of time should be planned in advance.B.2. Smoking
Smoking, especially on high roofs, causes butts and ashes to spread around due to the wind. Smoking should not be allowed on the roof. If possible, it would be appropriate to make a closed area protected from the wind and ventilated for smoking on the roof (such as a small hut), to have a fire extinguisher in the environment, to have an ashtray for butts and to clean this environment periodically.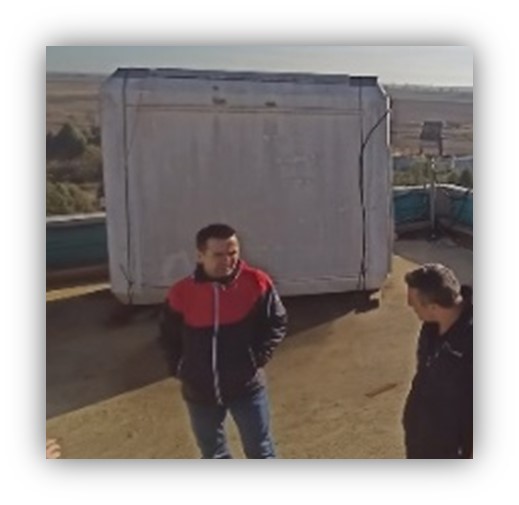
B.3. Placement of panels
If solar panels are not stored indoors and exposed to the sun in open areas, it may cause skin burns on the hands and body due to the heating of the irradiated surfaces of the panel during assembly and transportation. Therefore, it is important that personnel use protective gloves that provide protection against mechanical risks in outdoor work.B.4. Roof Lights
The lighting partitions on some panel roofs, which are placed to make more use of daylight, create a danger for the personnel working on the roof to fall from height. It is important that these gaps are identified before the start of field activities and made visible by surrounding them with warning tapes. If the roof material and the location of the panels are suitable, it would be more appropriate to build a barrier.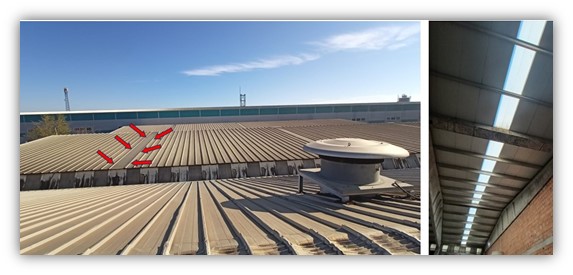
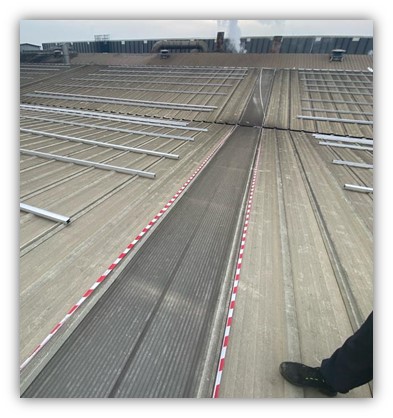
B.5. Sloped Roofs
A lifeline system must be installed to prevent personnel from falling from heights on sloping roofs and/or roofs without railings/parapets on the edge. The lifeline installed must be in accordance with TS EN 363, TS EN 795, TSE CEN / TS 16415 standards, static calculation must be made, capacity must be determined and installation report must be submitted. While designing the lifeline, it should prevent the worker from falling from height, but should not prevent the installation of the panels.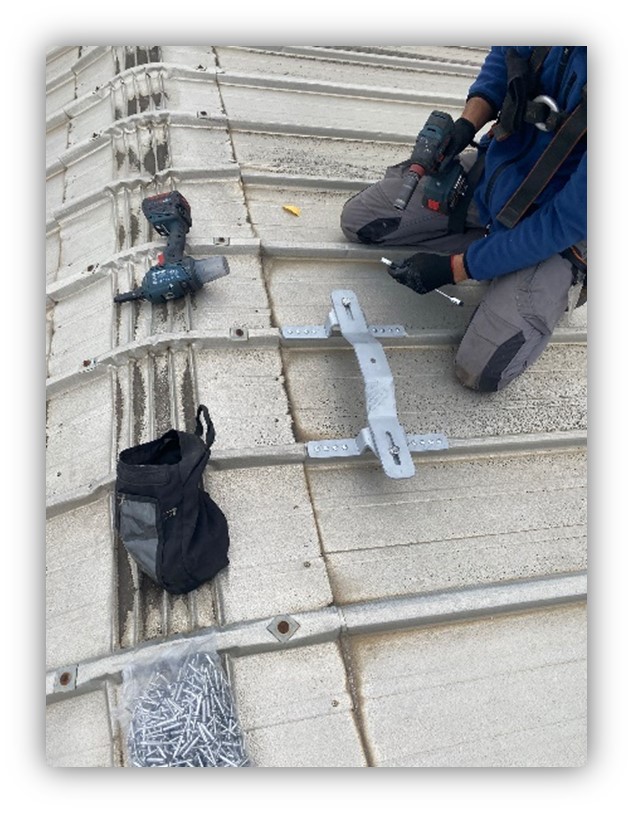

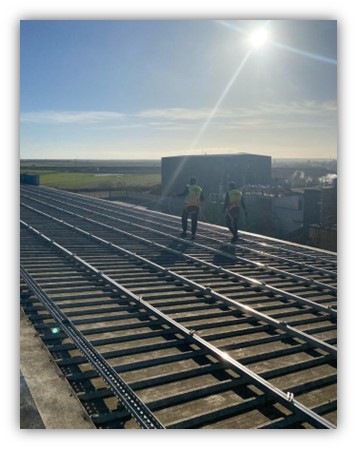